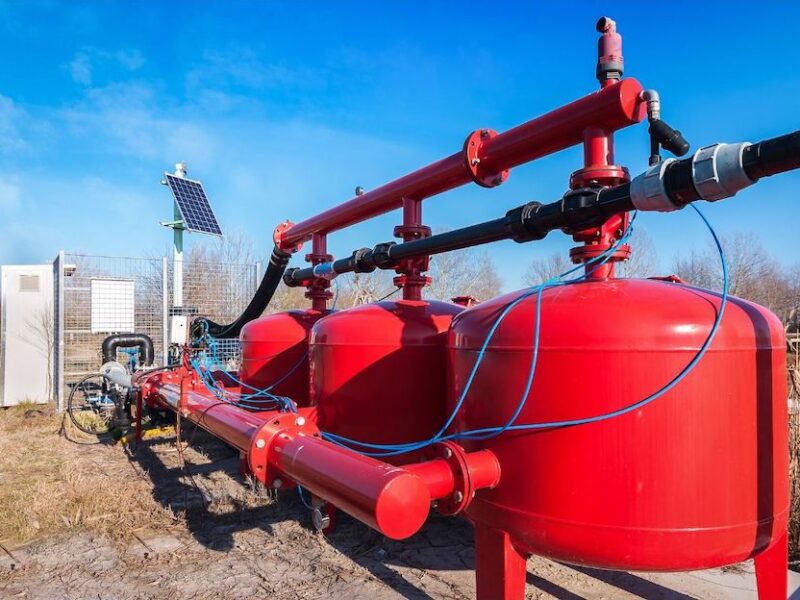
Especially for those of us in western developed nations, it’s extremely difficult to conceptualize that around 10% – or just under a billion people – do not yet have access to electricity. Even more surprising is the fact that the last few years’ worth of worldwide economic upsets have actually lost ground on global electrification, reverting some regions such as sub-Saharan Africa back a decade (about 20 million people lost access).
On the other end of the spectrum, westernized nations command incredible energy availability; even if it is naturally restricted to developed urban and rural areas. Between both extremes, a singular fact becomes pretty obvious: a significant proportion of livable land on the planet does not have readily available electricity.
It was with this observation in mind that a recent customer contacted Whitman to discuss a solar-powered water pump application. This client designs and manufactures solar pump systems intended to be deployed anywhere in the world where sunlight shines and water needs to flow. A necessary technical feature of these systems was that they would automatically shut down should they lose incoming water flow, and that was all we needed to know to determine that we could help.
About Us
As a veteran-owned small business, Whitman Controls is dedicated to supplying premium quality, reliable, technologically advanced instrumentation for use in nearly any application. Our Bristol, CT manufacturing facility embodies over 40 years of engineering, fabrication, and customer service expertise, serving both end-user and manufacturing customers nationwide through direct and distribution channels.
Application Summary
Solar pump systems have been a growing application niche over the last twenty years, providing commercial, academic, industrial, agricultural, and private users with fluid handling solutions where fixed power is not available. More so, current environmental concerns have further popularized solar pumps over legacy fuel-powered alternatives. A solar pump kit is rather straight forward – a photovoltaic cell (or solar panel) energizes a pump controller, which in turn powers a fluid pump so long as sunlight is available. Solar pumps are most commonly used in water wells supplying domestic, livestock, irrigation, and sanitation water in locations far away from power infrastructure, but also increasingly in developed areas when sustainability and cost-consciousness is a priority.
Pumps may be left to run for extended periods of time across a year without frequent user intervention, and as supply water levels fluctuate, these pumps can find themselves running without adequate incoming water, or ‘dry running’. After a short time of running dry, pumps can suffer heat buildup, mechanical wear, excess friction, and run-away rotation, all of which can damage the pump to the point of failure.
Challenge
In our initial introductory call, the customer made their goals abundantly clear:
- Develop an instrument-based, automatic solution that will reliably deactivate a pump experienced dry-run.
- Assure that this dry-run protection would trigger under varying scenarios leading to a loss of water prime – from seasonal water table declines to inlet blockage, physical pump damage to under-speed motor rotation. This meant that sensors involved would need to directly measure a process variable that would be present in all cases.
- Specify control components suitable for use in fully exposed outdoor environments pushing towards temperature, humidity, weather, and (naturally) sun exposure extremes.
- Design the control circuit to be super simple – operators and owners of these systems are often non-technical, and just need things to work.
We couldn’t thank the client enough for coming to the table with a very well-thought-out set of objectives, which allowed us to immediately jump into engineering review with our team. The client had tested a few early prototypes using pressure switches, flow switches, and point level switches, though none could consistently detect a dry-run condition across each possible scenario. The solar pumps varied in design as well, either using positive displacement or centrifugal heads, which further influenced measurable variables.
“We’re significantly growing our solar pump package sales year over year, all over the world. The worst thing that can happen is that somebody in the middle of nowhere depending on our pump set for their drinking water finds themselves with a burned-up pump because it ran dry. We needed a surefire detection method to make sure our kits were as reliable as they’re expected to be, but also so we could sleep at night given how many people depend on us.” – Product Manager, Confidential Solar Pump System OEM
Solution
Stepping back from simply throwing instruments at a test system, our engineering team turned their attention to the hydraulic interactions occurring in the pump head. After running a series of calculations and cross-checking against hydraulic models provided by the customer, we came to the definitive conclusion that measuring any variable involving the presence of water was not viable. With the right conditions, multiples scenarios could provide false-positive feedback when monitoring pressure, flow, level, or vibration variables, rendering all unacceptable. However, one variable in the calculations consistently returned a reliable value across all potential failure states: vacuum!
Whitman’s engineering team returned to the test station with a W117V Ultra Pure Stainless Steel Vacuum Switch in hand, and dug in for a thorough battery of test runs. In all tested scenarios, a slight vacuum was indeed detectable in the pump head any time a loss of incoming water occurred. In presenting the findings with our client, the W117V was locked in as the winning solution, based on its highly sensitive diaphragm (using a setpoint of 2 InHg), high temperature range (-65°F to 225°F), helium leak-tested quality control, and long-life stainless steel housing.
Results
With dry-run protection solved, our customer turned their attention to more pressing design opportunities. Next on deck, they wanted to streamline field deployment, helping to make their solar pump kits accessible to even the most remote, underdeveloped regions where technical installation support was entirely nonexistent. Whitman’s dry-run protection instrumentation was the first step in that direction, now to be followed by simple plug-and-play electrical wiring and erector-set style panel framing. We’re grateful to have played a small role in spreading solar-powered water systems to users far and wide, and can’t wait for the next chance to support such beneficial, sustainable, and humanitarian technologies.
Data Bullets
- 99.9% reliable dry-run detection and automatic pump shut off
- 35% fewer field support calls after adopting onboard dry-run protection
- 30 year average solar pump lifespan when equipped with integrated dry-run protection
Here at Whitman Controls, our values drive us to provide the highest level of servant partnership that you can find. To discuss your applications or to learn more about our capabilities, please contact us at (866) 556-5634, via email at info@whitmancontrols.com, or online at www.whitmancontrols.com