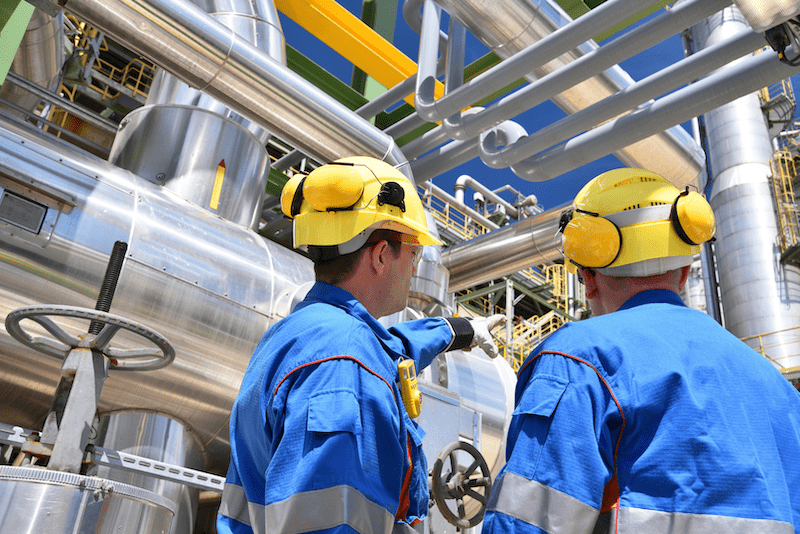
Our daily lives are built around products and energy sources derived from crude oil, and a whole lot of it at that. The global Oil & Gas Industry pumps out approximately 100 million barrels of crude oil per day, which in turn gets split into about 65% for transportation fuel, ~20% for petrochemical products, and ~15% for heavy and light oil products.
Recently, a midstream energy producer contacted Whitman to discuss an application that sought to optimize these proportions towards cleaner burning, more efficiently produced end-products. The issue at hand was inaccurate, high cost, high maintenance level control in the customer’s existing distillation feed tanks, stemming from the unique properties of their custom crude oil blends. Good thing custom level control is right up our alley!
About Us
As a veteran-owned small business, Whitman Controls is dedicated to supplying premium quality, reliable, technologically advanced instrumentation for use in nearly any application. Our Bristol, CT manufacturing facility embodies over 40 years of engineering, fabrication, and customer service expertise, serving both end-user and manufacturing customers nationwide through direct and distribution channels.
Application Summary
The American Petroleum Institute uses a unitless API Gravity measurement to describe oil’s density in comparison to water – the higher the gravity (measured in degrees), the lower the density. Crude oil is described by gravity categories – Extra Light, Light, Medium, Heavy, and Extra Heavy crude oils.
The Light Crude category contains API gravities from about 31° to 45°, and crude volumes that fall between 40° and 45° are the most commercially viable as they can produce the best yield proportions of end products. This API gravity range equates to a density range of 824 to 800 kg/m3. For reference, water’s density is 1,000 kg/m3, which clearly demonstrates that this ideal Light Crude is quite a bit lower in density than water, and therefore calls for special fluid process control instrumentation.
We can also appreciate that crude oil densities fluctuate during extraction, adding another factor in selecting suitable process control devices.
Challenge
We received an inquiry from a large midstream energy customer looking to solve a particularly difficult challenge in crude oil volume control within their various global field process plants. Crude petroleum was captured directly from wellheads and piped to storage vessels prior to initial separation and distillation.
The customer was experimenting with novel blends that could potentially eek out quantifiable benefit in downstream yield splits – that is to say, if they could very tightly target unique gravities, they could experiment with custom distillation runs and thus maximize fuel production proportions over traditional methods.
The issue however was that their existing point level instruments were experiencing reaction lag with these lighter densities, as these devices were built with float arms and switching forces based on near-water specific gravity.
If the devices were calibrated (by adding or removing weights) for certain gravities, the switches would then further mis-read when gravities were swung in the opposite direction. Worse, the existing level switches were expensive as they were made of stainless steel material, which also suffered mild corrosion from the sulfur, chlorides, and organic acids in the crude oil.
“[Our company’s] chemical engineers developed a very promising distillation profile that would get us more fuel-grade yields per pass, so long as we fed the column a precise gravity. The problem was that we couldn’t get the feed balance tanks to cycle correctly, constantly hitting high alarm, because the level switches couldn’t handle the lighter feed. Whitman’s [L20] poly level switch cured that as soon as they were installed.” – Field Refinery Application Engineer, Confidential Midstream Energy Group
Solution
Always up for a new challenge, Whitman’s engineers went straight to work. After a thorough application review with the customer, we narrowed the problem set down to two core design criteria.
- Minimum Specific Gravity: based on the customer’s desired API gravities, we knew we needed a sensor that would operate without fail down to about 0.74 specific gravity.
- Wetted Material: hearing about the existing stainless steel’s corrosion issues (and the associated high cost), we next knew that we needed a polymeric material that was compatible with all of the aggressive chemical components found in raw crude.
After a day of application engineering research and literature review, Whitman’s engineers landed on our L20 Polypropylene Side-Mounted Liquid Level Switch for this application.
We held a workshop meeting with the customer, consulted various chemical compatibility resources and verified against our own material certificates of conformity, confirmed specific gravity conversions from API gravities, checked off electrical and connection options, and finally reviewed commercial details.
From this workshop, the customer responded that they were pleased with the recommendation, and with nothing left to double-check, they placed an order for a bundle of L20 Switches to be sent directly to their R&D field refinery.
Results
At the time of this writing, the initial batch of L20 Polypropylene Level Switches have been installed into the customer’s crude distillation feed system for going on six months, without a single incorrect signal and no signs of corrosion. We are now working to standardize all of the customer’s feed balance tank systems to the Whitman L20 around the world, which will be an ongoing project slated to take the rest of the year.
Once complete, additional projects are already in the works, as the polypropylene material option has piqued the interest of several of the customer’s field operations managers looking to solve other process control challenges. The next time we’re at the pump filling gasoline into our own vehicles, we’ll remember this project and how a seemingly straightforward level control upgrade is today indirectly helping extract more usable fuel per barrel of crude oil for users all around the world.
Data Bullets
- 6% more useable fuel-grade products extracted per oil barrel using the customer’s new distillation process
- 100% accurate level switch performance since installation
- 71% unit cost savings compared to prior stainless steel version
- 2-Day lead time on stock L20 Polypropylene level switches
Here at Whitman Controls, our values drive us to provide the highest level of servant partnership that you can find. To discuss your applications or to learn more about our capabilities, please contact us at (866) 556-5634, via email at info@whitmancontrols.com, or online at www.whitmancontrols.com.