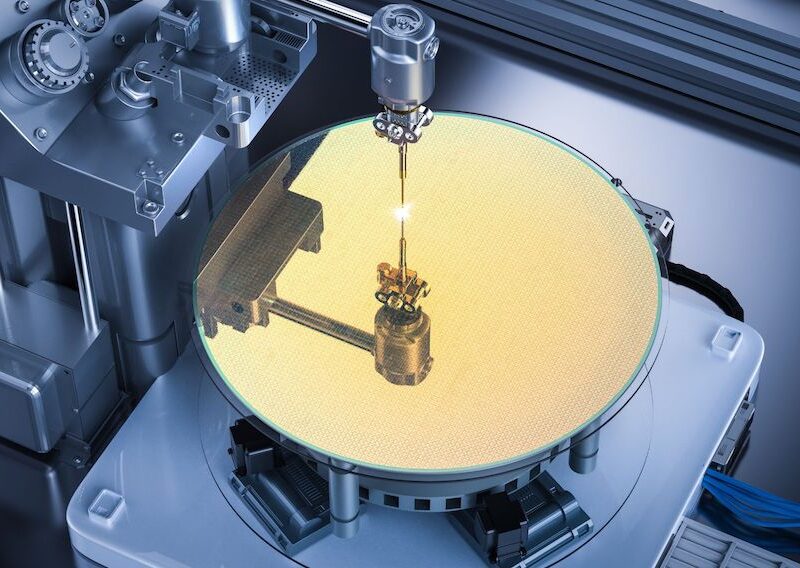
Integrated Circuits (or ICs) are the root of most of the technology we rely on in our daily lives, from mobile phones to internet data center servers to communication satellites in orbit. For commercial and industrial businesses, ICs provide the computational power found in all automated equipment and software systems as well.
Manufacturing ICs falls within the domain of the semiconductor industry, where all circuit boards, processing chips, and transistor arrays are produced. Semiconductor manufacturing is extremely complex, operating within a scale of nanometers (down to molecular structures measuring just 10 atoms wide).
At these scales, even the tiniest unwanted particulates can result in product reject scenarios, such as by plugging up physical wafer structures, causing coatings and films to misapply, and shorting out electrical circuits.
With combating these unwanted particulates in mind, a manufacturer of ozone cleaning equipment recently contacted Whitman to discuss ozone process control solutions that would outperform traditional technologies while also providing a host of environmental and efficiency benefits to the semiconductor industry at large. Help the entire industry, you say? Let’s go!
About Us
As a veteran-owned small business, Whitman Controls is dedicated to supplying premium quality, reliable, technologically advanced instrumentation for use in nearly any application. Our Bristol, CT manufacturing facility embodies over 40 years of engineering, fabrication, and customer service expertise, serving both end-user and manufacturing customers nationwide through direct and distribution channels.
Application Summary
Ozone gas molecules are made up of three oxygen atoms, formed by exposing oxygen to UV light or electrical current. Ozone gas’ volatility provides a natural cleaning function – when ozone contacts another organic material, it gives up its third oxygen atom to that material, which then oxidizes (or breaks down) the unwanted molecule it attached to. In industrial applications, ozone is generated from an oxygen source and then used as a cleaning agent in gas or fluid form.
Ozone is used to rinse, wash, mist, or blow off all varieties of surfaces, products, and materials with the goal of disinfecting them via oxidation. In Semiconductor manufacturing, electronic circuit assemblies must be thoroughly rinsed of organic particles in order to avoid contamination and short circuits. Ozone cleaning is a rising alternative over traditional chemical processes, achieving the same or better results of removing organic contaminants while also drastically cutting costs and environmental impacts.
Challenge
Our client’s line of ozone equipment was originally designed for food and beverage, water, and wastewater treatment applications, all of which operate at a higher volume, wider accuracy band than called for by semiconductor projects.
This equipment consists of an oxygen concentrator that feeds high-oxygen gas into an ozone generator, which then sends ozone gas to a storage tank where it will reside for a short amount of time before being injected into a purified water stream. This ozonated water stream is then routed out to equipment for cleaning, rinsing, or spraying processes.
By analyzing the equipment’s existing control components, we identified three main challenges that we’d need to overcome to best target semiconductor applications, as follows:
1. Proportional Concentration Control: higher flow rates can be controlled by volume and time well, but for the smaller flows and tighter accuracy demands of semiconductor applications, we were more inclined to directly control for ozone concentration.
2. Lower Limit Safeties: since it is very difficult to cross-check the efficacy of a semiconductor cleaning process at the nanometer level after the fact, it is imperative that cleaning processes occur per their specifications in-situ. This added much greater sensitivity to any under-cleaning situations, specifically low pressure, flow, and contact time conditions.
3. True Continuous Operation: unlike the client’s other applications that operate in batch cycles with ample idle time between batches, semiconductor applications require true continuous operation. Process controls would need to be highly repeatable, dependable, durable, and resistant to drift.
“Ozone is an excellent oxidizer with zero environmental contamination, zero waste to deal with, and none of the chemical hazards that operators are normally exposed to. We’re quickly replacing chemical cleaning and treatment steps with ozone throughout electronic fab [facilities], and customers are saying that their payback is paid by chemical savings alone, not even considering their reduced energy and wastewater costs, and all the avoided rejects and rework.” – Vice President of Sales, Confidential Ozone Equipment Manufacturer
Solution
After our application engineers reviewed our ideas with the client, our respective teams agreed on a course of action and got to work. The client’s team constructed a pilot test system on their end, and Whitman’s team assembled an instrument package to be installed and vetted in that test rig. Test runs were conducted successfully within a few weeks, and the team locked in a set of mechanical, instrumentation, and programmatic features that would round out a semiconductor-specific version of the client’s ozone system platform.
Our instrumentation package incorporated key features necessary to meet all the demands of semiconductor ozone applications, including:
- Stainless steel materials, to withstand the oxidizing effects of ozone
- High pressure ratings, to protect against any exposure to high incoming oxygen gas pressure
- Ultra-simple construction and electronic circuitry, so as to maximize reliability and repeatability
- Factory configured, non-adjustable set point, so as to eliminate risk of field setpoint changes, as well as to minimize drift
- High temperature rating, as some rinse applications are also preheated to avoid wafer shock
- Compact format, to keep system footprints small, especially for mobile and on-machine equipment mounting
- Compound sensor technologies such as combining vacuum and pressure switching in a single instrument, further minimizing system complexity and footprint
Results
After pilot trials concluded, our client launched and sold multiple ozonated water systems into semiconductor applications such as raw material rinsing, wafer pre-coat rinsing, coating water sterilization, and general equipment cleaning.
Ozone’s disinfecting and zero-residue properties have helped displace multiple legacy chemical processes in these facilities, saving chemical and heating costs, waste treatment, and environmental impacts abound. Our client is now looking to expand into central utility ozone applications for their semiconductor customers (such as cooling tower water and process air treatment), with our continued support on process control and instrumentation elements.
Data Bullets
- 75% reduction in cleaning chemical use by replacing with ozonated water
- 15% reduction in process steps via in-place ozone rinsing vs separate chemical rinsing
- 1-2 lead time on ozone-compatible instrumentation
- 12%+ semiconductor industry projected annual growth rate from 2023 to 2029
Here at Whitman Controls, our values drive us to provide the highest level of servant partnership that you can find. To discuss your applications or to learn more about our capabilities, please contact us at (866) 614-9236, via email at info@whitmancontrols.com, or online at www.whitmancontrols.com.